在實行cnc加工程序前主要先進行對刀以肯定起始點位置,而對刀通常是操縱者頗感頭痛的事情,刀具刃磨后又要從頭對刀,刀具的刀尖磨損,獨特是多把刀進行加工時,還需測刀補值。
1.點動對刀發
cnc加工設備按管制面板上的點動鍵,將刀尖輕觸被加工件表面(X和Z兩個目標分兩次進行點動),計數器清零,再退到需設定的初始位置(X、Z設計初值),再清零,得到該刀初始位置。依序肯定每把刀的初始位置,經試加工后再調節到準確的設計位置(起始點)。這種方式無須任何輔具,唾手就可操縱,但時光較長,獨特是每修磨一次刀具就一定從頭調節一次。
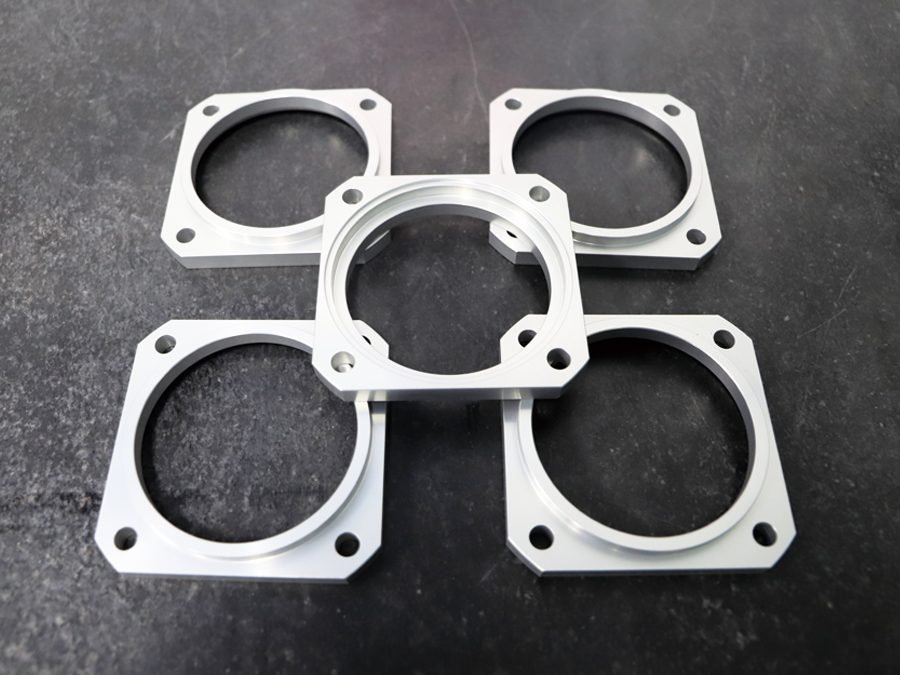
2.選用對刀儀
現在很多車床上都裝備了對刀儀,運用對刀儀對刀可罷免丈量是發生的偏差,大大升高了對刀精度,由于運用對刀儀不妨自動計算各把刀的刀長和刀寬的差值,并將其存入體系中,在加工此外的零件的時辰就只需求準則刀,如此就大大節儉了時光。需求關注的是運用對刀儀對刀通常都沒有準則刀具,在對刀的時辰先對準則刀。其缺點是選用對刀儀需求添置對刀儀輔助設備,本錢較高,裝卸費力。
3.選用數控刀具
cnc加工刀具安裝初次定位后,在進過一段時光切削后發生磨損而需求刃磨,尋常刀具刃磨后從頭安裝的刀尖位置發生了轉變,需求從頭對刀,而數控刀具的特點是刀具制造精度高刀片轉位后反復定位精度在0.02mm控制,大大減少了對刀時光,同時,刀片上涂有金屬層(Sic、Tic等)使其耐用度大大升高,可是這個本錢也有點高。
4.用對刀塊對刀,選用自控對刀法
用塑料、有機玻璃等制成的簡單對刀塊課簡便的完成刀具刃磨后的反復定位,可是定位精度較差平常在0.2~0.5mm,單任不失為一種迅速的定位方式,再用調節就可以很快很簡便。